Industry 4.0
Industry 4.0 is a concept first developed in 2010 in Germany to describe a vision of industrial manufacturing with all its processes interconnected through the Internet of Things (IoT: Internet of Things).
Also known as the Fourth Industrial Revolution, it consists of the digitalization of industrial processes through the interaction of artificial intelligence with machine tools and the optimization of resources, focused on the creation of effective commercial strategies that guarantee customer satisfaction and the personalization of services.
What Industry 4.0 offers through digitization and the use of connected platforms can be summarized as:
- A constant ability to adapt to demand.
- Serving the customer in a more personalized way.
- Providing a personalized after-sales service to the customer.
- Designing, producing and selling products in less time.
- Adding services to physical products.
- Creating shorter and more profitable production runs.
- Leveraging information for analysis from multiple channels, and using it in real time.
Industry 4.0 is often associated with the term IIoT (Industrial Internet of Things), manufacturing that integrates production and physical operations with digital technology, machine learning and big data to create an integrated and highly connected ecosystem focused on product and supply chain management.
Key Technologies in Industry 4.0
The expansion of the Fourth Industrial Revolution through Industry 4.0 cannot be understood without its relationship with the main technologies that make it possible. In this sense, the following can be highlighted:
Internet of Things (IoT: Internet of Things): industrial machinery is able to communicate and share in real time information collected through multiple sensors. This enables a deeper analysis of the entire system and an immediate response to any event.
Big data, artificial intelligence and machine learning: these three disciplines are deeply related to the collection and management of a huge volume of data from different sources, providing the possibility of automatic learning based on a history of data and repetition of operations, and allowing corrections to processes.
- Augmented reality: allows adding layers of virtual information to real environments. Through electronic devices, such as glasses or screens, users access a mixed reality where real elements are combined and complemented with virtual ones.
- Digital scenarios: this technology uses data from the physical world to recreate a virtual environment. With this approach, it is possible to study a problem or test operation of a system digitally, and then apply the solution in the real world.
- Blockchain: this is a new way of structuring the transmission of data, distributed in encrypted blocks linked to each other and identified with unique and non-repeatable numbers. Based on complex mathematical algorithms, this system ensures the inviolability of the information by being able to detect and reject any unauthorized changes.
- Cloud computing: the need to interconnect more and more systems and links in the supply chain makes Software in the Cloud (SaaS: Software as a Service) an almost essential element, as it facilitates access to information from anywhere and integration with other applications, as well as the execution of automatic updates that reinforce cybersecurity.
- Logistics Traceability: having precise control over the information related to logistics processes is essential, since it allows knowing at all times where and in what state the product is. Automatic identification with RFID technology (Radio Frequency Identification), for example in warehouses, allows to improve the accuracy and speed of inventories of parts and products.
- Warehouse robotization: the design of autonomous systems capable of speeding up the loading and unloading of goods, as well as the transfer of products and their location on the shelves, has optimized the flow of materials and personnel within the facilities and boosted internal logistics as an engine of growth.
On the way towards Industry 4.0
Industry 4.0 is a new way of automated, independent and controllable production from anywhere. It employs machinery, devices and specialized personnel, all connected and communicating with each other, uses sensors to collect data from the physical world, and automates operational and risky tasks, as well as simple decisions and responses.
What enabled these changes in the industry was the reduction of sensor costs, data storage and process connectivity. The benefits for businesses include:
- More flexible production: it is possible to plan and intervene in each link of the value chain of a product without altering the others.
- Increased efficiency: production in modules that are assembled in less time.
- Logistics optimization: algorithms can calculate ideal delivery routes to avoid congestion, disruptions and delays, as well as improve the flow of goods.
- Personalized products: smart products allow real-time usage data to be sent to the manufacturer to improve the customer experience and create new products and services based on that information.
- Predictive analytics: the use of data is the basis for new services that predict the wearing of a product or element of a system.
Challenges of Industry 4.0
The new concept of Industry 4.0, associated with the Fourth Industrial Revolution, is expected to be capable of driving fundamental changes similar to those of the three preceding revolutions: the First Revolution introduced mechanics powered by water and steam, the Second Revolution introduced electricity and mass production, and the Third Revolution introduced automation and the proliferation of information technologies.
Some of the most important challenges that businesses and organizations implementing Industry 4.0 are going to face include:
- Developing analytics systems that turn the deluge of data produced by smart factories into useful and valuable information.
- Responding to current issues related to energy saving and natural resource management.
- Cybersecurity, because although organizations in the industry sector are confident in their ability to protect themselves, cyber attacks prove otherwise. IT security has become one of the main strategic objectives of the industry, because when it is compromised, it not only affects reputation of an entity, but fundamentally its productivity.
- Avoiding failures in computer or communication systems that could result in large economic losses.
- High technology infrastructure costs.
- Lack of qualified personnel to lead companies into the Fourth Industrial Revolution.
- Reluctance of senior management to embrace the digital transformation of their businesses.
- Reduction and specialization of jobs due to the automation of processes, which will lead to an inevitable professional reconversion, adapting to new jobs that will arise with the change of paradigm.
Industry 4.0 is not just about investing in new technology and tools to improve manufacturing efficiency, it is about revolutionizing the way a company's entire organization operates and grows.
On the other hand, and increasingly, cybersecurity is preventing companies from entering Industry 4.0, because the threats posed by cyber attacks are no longer invisible. Technical, organizational and human weaknesses in companies can open several doors to cyber attacks.
This aspect, due to its importance, must be strongly taken into account for the implementation of the new paradigm.
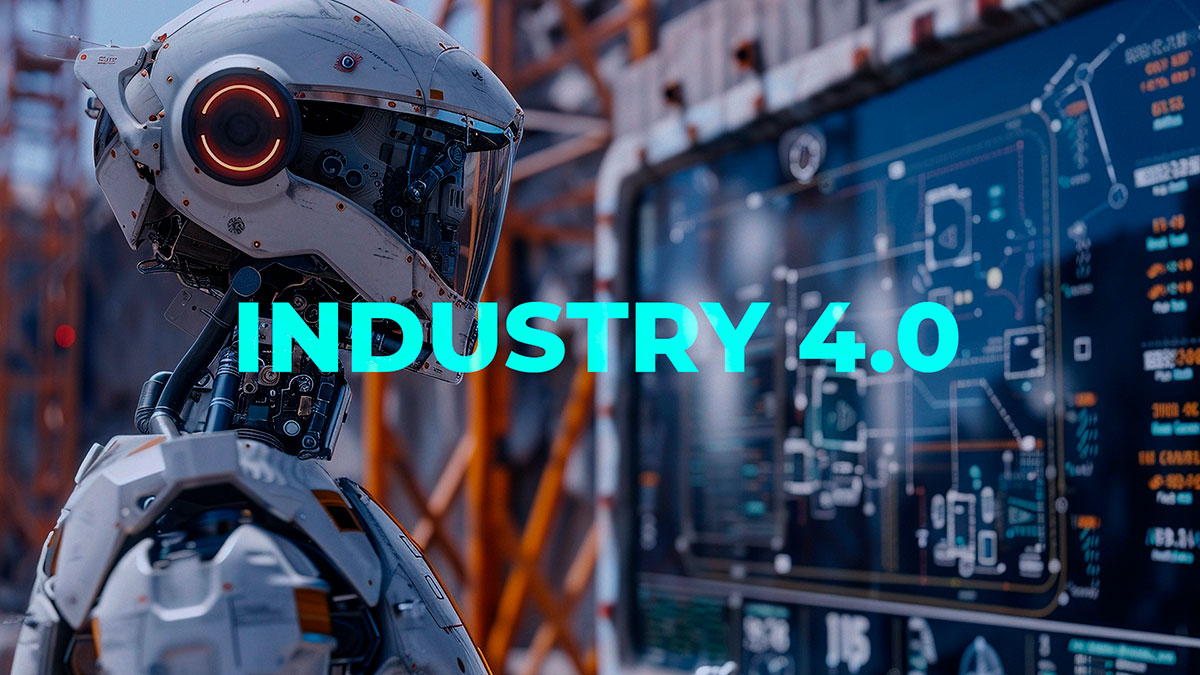